Najważniejsze jest jednak to, że pracę tych obszarów zleca się bezpośrednio przez rzeczywiste zapotrzebowanie kolejnych operacji, na bieżąco – a nie na podstawie planu ich pracy i to tworzonego w biurze, z co najmniej jednodniowym wyprzedzeniem.
Harmonogramy operacji w procesie produkcji
Analiza kosztów całkowitych wykazuje, że produkty stanowiące znikomy udział w portfelu zamówień klientów i przy okazji przekładające się na niewielki zysk dla firmy są harmonogramowane przez ciąg sekwencyjny. Schematy często przedstawiają harmonogram pracy stanowisk dostarczających materiały do kolejnych operacji. Oprócz operacji produkcyjnych, mogą do nich należeć zarówno operacje magazynowe, jak i transportowe.
Należy odrzucić wszelkie ograniczenia, które do tej pory wpływały na pracę i powodowały, że trzeba było żmudnie uwzględniać je w swoich planach, i które tak często destrukcyjnie wpływały na ich wykonanie. Dopiero będąc uwolnionym od złych przyzwyczajeń, można usiąść przed czystą kartką papieru, na której znajduje się cel: satysfakcja klienta, czyli zrealizowane zamówienie. I to zarówno klienta zewnętrznego, jak i wewnętrznego, którym jest każda operacja produkcyjna i który uczestniczy w procesie dodawania wartości dla klienta zewnętrznego.
Jeśli w ten sposób spojrzy się na ten proces, będzie można ujrzeć, że ogniwa wzajemnie od siebie zależne łączy prosta relacja: dostawca – klient. W takim ujęciu łatwiej zmienić stary sposób pracy i rozpocząć nową erę, w której harmonogramowanie produkcji odbywa się samoczynnie na podstawie rzeczywistego zapotrzebowania klienta.
Zanim przystąpi się do zmiany sposobu harmonogramowania w całym zakładzie, zanim dokona się wyboru spośród dwóch odmian systemu Pull, tego, który będzie najlepszy – pełny czy sekwencyjny, należy przeprowadzić dosyć szczegółową analizę trzech głównych obszarów: klienta, dostawcy i pętli zasilania.
W zależności od złożoności procesu produkcyjnego być może taką analizę będzie trzeba wykonać dla każdej pary procesów wzajemnie ze sobą połączonych relacją dostawca – klient:
-
Analiza zapotrzebowania klienta, czyli w omawianym przypadku stanowisko spawania.
-
Określenie możliwości dostawcy, czyli w omawianym przypadku stanowisko cięcia prętów.
-
Wyznaczenie pętli obiegu informacji oraz ścieżki transportu, które połączą te dwa stanowiska.
Przechodząc przez kolejne obszary, będzie można określić, jakim wymaganiom musi sprostać każde ze stanowisk produkcyjnych oraz jak zaprojektować zasilanie w materiał, aby osiągnąć stuprocentową satysfakcję klienta przy najniższym z możliwych kosztów. Być może zanim firma będzie w stanie realizować zamówienia klienta w wymaganym „lead time” bez utrzymywania zapasu wyrobu gotowego bądź półproduktów lub materiałów, będzie trzeba utrzymywać niewielki zapas.
Zobacz także:
Tagi: produkcja
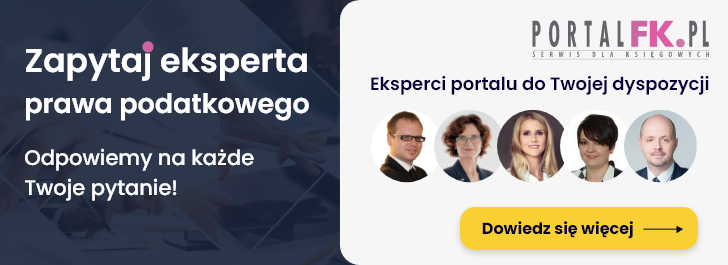